SESSION 11
INVERSE RADIATION PROBLEMS II
INVERSE DESIGN Of RADIATING ENCLOSURES WITH AN
ISOTHERMAL PARTICIPATING MEDIUM
Juan Carlos Morales*,
Vigain Harutunian*, Masahito Oguma**,
and John R. Howell*
*Department of Mechanical Engineering, The University of Texas at
Austin
**IHI Research Institute, Inc., Yokohama, Japan
Standard analysis of radiative transfer in enclosures with participating media
defines a geometry and a specified temperature or energy flux distribution on
each surface. The temperature or temperature distribution in the participating
medium within the enclosure may also be given. Unknown temperatures and fluxes
are then computed. Here, an inverse design procedure is described for radiating enclosures containing an isothermal participating medium. In inverse design,
both a temperature and heat flux distribution are given for one enclosure
surface (the “design” surface), as would be the case for heat treating furnaces and applications where conditions are required on a particular surface to meet
process needs. On one surface of the enclosure, no conditions are imposed;
these are then determined from the conditions required on the design surface.
The inverse problem requires solving a Fredholm equation of the first kind,
which is notoriously ill-conditioned. Description and examples are given of one useful technique.
Solutions are shown for the necessary emissive power distribution on an
enclosure surface that will provide a specified temperature and heat flux
distribution on another enclosure surface. Effects of the temperature and
absorption coefficient of the medium within the enclosure are shown, as are the effects of enclosure aspect ratio and surface properties.
The methods for ascertaining the accuracy and approach to oscillatory solutions inherent in this type of problem are discussed, and the behavior of the
singular values is shown to be a useful tool for reducing the numerical labor
involved in the solution.
Some useful solutions are presented that could not be generated by the usual
radiative analysis techniques without multiple iterative solutions of the
radiative energy equations.
It is argued that inverse solutions present a very useful tool for the thermal
analyst, particularly for problems where radiative transfer is a dominant
energy transfer mode.
SOLUTION OF THE INVERSE RADIATIVE LOAD PROBLEMS
BY THE SINGULAR VALUE DECOMPOSITION
Kazuhiko Kudo, Akiyoshi Kuroda, Amr Eid,
Takahiko Saito
Department of Mechanical Engineering, Faculty of Engineering, Hokkaido
University
N-13, W-8, Kita-ku, Sapporo 060, JAPAN
and
Masahito Oguma
Advanced Technology Department 2, Research Institute, Isikawajima-Harima Heavy
Industries Co., Ltd.
1, Shin-Nakahara-cho, Isogo-ku, Yokohama 235, JAPAN
A method is developed to solve inverse radiative load problems. The method
estimates the heat load distribution and temperature profile within gas region
from the values of wall temperature and heat flux distributions, while the
shape of the analytical domain and the profile of the optical property values
within the system are given. The method can treat arbitrarily shaped
multi-dimensional systems with mass flow. In the method, the system is divided
into many gas and wall elements, and the radiative heat exchange between each
element is calculated by using the MonteCarlo method. By using the results and
the mass-flow distributions, the energy equations for each elements are
expressed by a matrix form. When the values of the heat-load distribution
within the gas region and temperature profile along the wall are given, a set
of the matrix equations can easily be solved to obtain the profiles of the gas
temperature and wall-heat flux. This is called as forward problem. To obtain
the heat-load distribution from the profiles of the temperature and heat flux
along the wall: inverse radiative load problem, the matrix which relates the
gas temperature to the wall-heat flux should be converted into the inverse form. Due to the ill- posedness of inverse problems, the matrix inversion is usually
difficult by using ordinary methods and/or obtained inverse matrix gives very
fluctuating results. In the present study, the inverse matrix is obtained by
singular value decomposition method.
To check the validity of the method, a forward problem is solved by giving an
arbitrarily distributed heat load within a square gray-gas region of 10mx 10m
surrounded by gray walls with a temperature of 300K to obtain the corresponding wall-heat-flux distribution. Then, the inverse problem is solved by using the
present method by giving the resulting wall-heat flux as the input, and the
heat-load distribution within the gas region is estimated. The heat-load
distribution obtained from the inverse problem fits very well with those given
to the forward problem, which shows the validity of the present method for
solving radiative heat-load problems.
By using the method, the radiative heat-load distribution within gas region
satisfying the constant heat-flux condition along the wall is also obtained
when the condition number of the matrix is reduced to an appropriate lower
value by setting some singular values to be 0. The wall-heat flux obtained by
using forward problem by giving the resulting heat-load distribution is almost
constant with only 1% fluctuations.
The present method can be used not only to estimate the heat-load distribution
within furnaces, but also be applied to the problems to decide an optimum
burner arrangement within furnaces satisfying prescribed heat-flux profiles.
RETRIEVAL OF ABSORPTION AND TEMPERATURE PROFILES IN
PREMIXTED FLAME BY INVERSE RADIATIVE METHODS
M. Sakami and M. Lallemand
Laboratoire d'Etudes Thermiques (URA 1403 CNRS)
ENSMA 86960 Futuroscope, France
Spectral absorption and temperature profiles in a cross section of a premixted
propane-air flame have been carried out by inversion of the radiative transfer
equation (RTE) from simultaneous directional transmission and emission
measurements.
The central element of the experimental setup is a Fourier Transform Infrared
Spectrometer working at 4cm-1 resolution. In a given optical line of
sight of prescribed optical extension it receives selected angular radiation
coming up either from an external source crossing through the flame or from the emission of the flame itself. A black body at 1200K allowed the intenity
calibration. The propane-air flame is produced by an axisymmetric burner in
which the gases are mixted in a tranquilizer and homogeneizer chamber. Its
richness is fixed close to one.
In a given cross section, perpendicular to the symmetry axis of the flame
(of space dependent absorption coefficient kn(r), the outgoing
spectral directional intensity Ln(p) in the line of sight
to, characterized by the positionning parameter p, can be written
as
(1)
where R is a working radius, u=p (see Fig.1), Lno(r) the
Planck function and An(u) is the transmission which is related to
the absorption profile by the relationship:
(2)
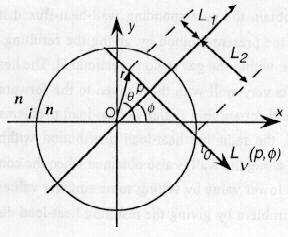 Fig.1-Geometry in a flame cross section
Both absorption coefficient and the temperature profiles settled up in the
medium may be retrieved as solutions of the coupled Volterra integral equations (1) and (2) when the projections sets An(pi) and
Ln(pi) are known from measurements, with i=1...20.
For the resolution of these ill-posed inverse radiative problems several
methods of inversion have been used: the Abel inversion with data
preconditionning, the Regularised-Adjoint-Conjugate-Gradient method, the
Mollification method and the Fourier-Bessel inversion method. They were
associated with special filtering and symmetrization techniques.
As a result in the lower part of the flame the absorption profiles of propane
and CO2 have been reconstructed at 2980 cm-1 and 2280
cm-1, respectively, in a satisfactionning way and the CO2 profile
may be recovered at the top of the flame. Similarly, the temperature profiles
have been retrieved and the results tested with thermo-couple measurements.
APPLICATION OF PHYSICAL AND OPTICAL METHODS FOR SOOT
EVALUATION IN A FULL-SCALE POWER PLANT
Loretta Bonfanti*,
Leonardo Castellano**, Sauro Pasini*,
Nice Pintus*,
Christine Mounaim-Rousselle***
*ENEL-CRT, Pisa, Italy, **MATEC, Milano, Italy,
***present address: L.C.S.R. CNRS, Orleans, France
Over the last few years, increasing attention has been paid to the problem of
reducing pollutant emissions from the combustion processes of fossil fuels. To
meet the requirements concerning Nox emissions, techniques based on a fuel/air
staging were utilized. It is not difficult to imagine that the effectiveness of
these techniques is very dependent on boiler configuration (boiler type, excess oxygen level, burner zone heat release rate, rate of fuel air mixing,
atomization quality and others) and, at the same time, these new combustion
configurations can have an impact on the thermal performance of the boiler
itself.
Strong efforts have been dedicated to improve the knowledge on the methods for
clean combustion, but many topics in the description of the physical behavior
of a full-scale plant have not yet had a satisfactory solution. The present
paper deals with one of the most important problems encountered in evaluating
the performance of advanced low-pollutant combustion systems: the measurement
of the concentration of combustion products that exist in form of solid
particles (soot) in the combustion chamber. Experimental tests were conducted
on an oil-fired 150 Mwe power station (Livorno unit#1). The basic idea of the
study was to develop and verify the compatibility of different techniques for
measuring the extinction coefficient and volume fraction of soot in furnace.
The main conclusion is that a rough theoretical analysis of the data collected
by two optical methods and the information given by the application of a Lidar apparatus provide almost similar values. More detailed information available
from chemical analysis, which is not yet completed, could prove to b crucial to
corroborate or disprove this statement.
TUBE LEAKAGE FFECT ON RADIATION HEAT FLUX IN BOILER
Neven Duic, Zeljko Bogdan,
Daniel Rolph Schneider, Naim Afgan*
Faculty of Mechanical Engineering and Naval Architecture
University of Zagreb
*Instituto Superior Tecnico
Technical University of Lisbon
A common failure in the boiler furnace is tube rupture. It may cause large
financial losses. An early diagnostics of tube leakage would help in preventing the failure by planning maintenence. For this reason it is of the importance to have the detection system which will give an early warning for the eventual
development of the tube rupture. The detection system should be based on the
reading of the selected variables which are dependent on the water leakage mass
content in the flue gases. In the vicinity of the tube leakage the
concentration of water vapor is increased and heat flux density distribution on
the furnace wall changed. The degree of change is measure of the incident.
The aim of this paper is to investigate the sensitivity of the radiation heat
flux changes due to the water leakage into the furnace. The zone method based
mathematical model was developed in order to enable that analyses. The
three-dimensional mathematical model describes steady-state behavior of the
steam generator furnace using PISO numerical algorithm for solving conservation equations. Nine conservation equations for each control volume, including
continuity, momentum, enthalpy and mass transport of fuel, oxygen, carbon
dioxide and water vapor are used for determination of the temperature, velocity and concentration distributions. The combustion model is described by overall
reaction rate. Solution of each conservation equation is obtained as a
quasi-linear system with the additive correction multigrid technique. The Monte
Carlo method is used to calculate radiation heat transfer between elementary
gas and surface zones. Radiation properties are obtained by three grey gases
model. The flue gas mixture radiation properties are primarily influenced by
water vapor and carbon dioxide content. Boiler furnace behavior simulation
results of the tube leakage conditions are represented graphically and compared with the normal operating conditions. It was shown that the radiation heat flux is sufficiently sensitive to detect the water leakage into the furnace.
|