SESSION 5
MASS TRANSFER IN LIQUID-LIQUID SYSTEMS
Chairmen: T. Özbelge, Y.H. Mori
FLOW OF HIGH INTERNAL PHASE RATIO EMULSIONS THROUGH PIPES, ORIFICES AND NOZZLES
Sümer Peker, Tamer Tanilmis, Rifat Özsaygi, Ekrem Tekden Ege University, Chemical Engineering Department, Bornova, Izmir, Turkey
ABSTRACT. The flow behavior of high internal phase ratio emulsions through pipes of 3.5, 5.6
and 21 mm internal diameters, orifices with Do / Di ratios of 0.2, 0.4, 0.6 and 0.8 and nozzles with
uniform decrease in diameter is investigated in this work.
1. INTRODUCTION
The use of high internal phase ratio emulsions (HIPRE) with drop volume concentrations greater
than 75% in foods, cosmetics and other applications has aroused interest in their complex rheological
behavior during the last decade. In high internal phase ratio emulsions, polygonal drop shapes
develop with increasing dispersed phase ratios. Formation of a network structure with planar films
between the dispersed phase cells leads to the development of yield stresses superimposed on the
power law behavior. Thus, Herschel - Bulkley model,
(1)
is generally used to describe the rheological behavior of high internal phase ratio emulsions (HIPRE)
under shear. In this work, shear flow of W/O type HIPRE in pipes and elongational flow in nozzles
and orifices are addressed.
2. THEORY
For shear flow in pipes the equation of motion was solved for the most general case of 1. power law
fluids, 2. presence of a yield stress 3. the presence of slip. The final equation obtained for the
average velocity, V, is,
(2)
Elongational viscosity is calculated from the pressure differential due to normal stresses
developed under constant extension rate , where the various terms are defined by the equations,
(3)
(4)
Orifice coefficients are calculated from the mechanical energy and total mass balance equations:
(5)
3. EXPERIMENTAL WORK
In the experimental set-up used, pipes of 3.5, 5.6 and 21.6 mm diameters were attached to the
bottom of a stainless-steel storage tank through an elbow connection so that the pipes and the
orifices would be horizontal. Two nozzles, 30 mm and 20 mm in length were used over which the
diameter decreased uniformly from 21 mm to 9 mm. Four different sharp edged orifices with hole
diameters ( 4, 8, 12 and 16 mm) corresponding approximately to Do/Di ratios of 0.2, 0.4, 0.6 and
0.8, respectively, were used in the experiments. 80, 88 and 94% W/O type emulsions were prepared
with 1%(wt) sorbitol solution as the dispersed aqueous phase, paraffinic oil with an empirical
formula of C17H36 as the continuous oil phase, polyoxyethylene (2) oleyl ether as the surfactant.
4. RESULTS
The main results for flow in pipes and orifices obtained in this work are plotted in Figures 1 and 2.
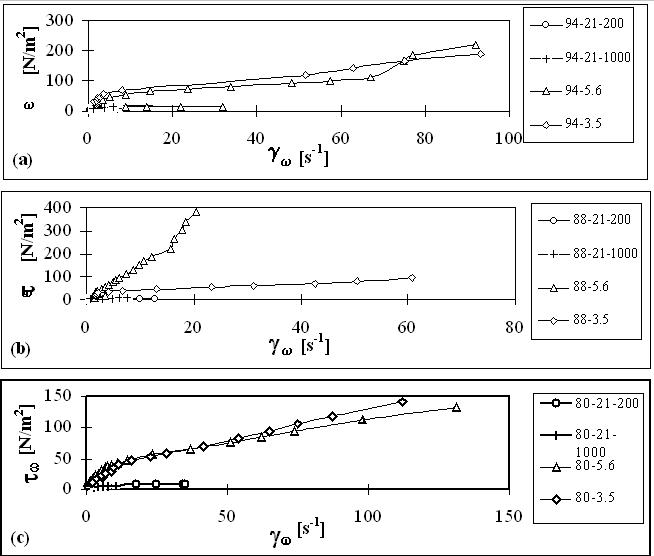
Figure 1. Variation of wall shear stresses with shear rate during the flow of HIPRE
a) 94 % emulsion, b) 88% emulsion, c) 80% emulsion
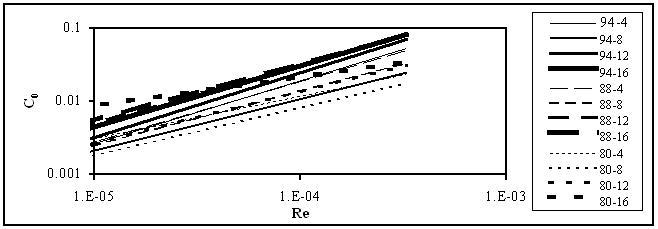
Figure 2. Variation of the orifice coefficients with Reynolds number
5. CONCLUSION
The experimental results obtained in this work confirm the inhomogeneity in the flow behavior of
HIPRE. At low velocities restructuring of HIPRE under shear stresses control its flow behavior. At
high velocities cell walls rupture to form a film at the walls over which the emulsion flows.
Experimental evidence obtained in this work points to the necessity of more work on dynamic
behavior of surfactant bilayers for a substantial understanding of the rheological behavior of HIPRE.
PREDICTION OF MUTUAL DIFFUSION COEFFICIENTS OF AROMATICS - BY GROUP CONTRIBUTlON METHOD
X. M. Guo, W. Y. Fei and J. D. Wang Department of Chemical Engineering, Tsinghua University, Beijing 100084, China
ABSTRACT
The diffusion coeffcient is an essential liquid transport property for the design of
liquid-liquid extractors. It becomes more important with the introduction and use
of the non-equilibrium stage model recent years, since the accuracy of prediction
of the mass transfer coeffcients is the key of the new model application[1,2].
However, experimentally determined diffusion coeffcients (especially for multi-ring
hydrocarbons) are scarce and the theoretical approaches to predict liquid diffusion
coeffcients are not accurate enough.
The prediction of diffusion coeffcients by group contribution method has been
proposed by Ye et al.[3]. According to this new approach, the molecular diffusing
area parameters and molecular diffusing activation energy are considered as the
factors which influence the molecular diffusion coeffcient. These factors are
evaluated by the contribution of the functional groups consisting the molecules in
the solution. By fitting a large amount of experimental data of self diffusion and
limiting diffusion coeffcients, the diffusing activation energy can be calculated.
However, the methods of defining the functional groups and obtaining the group
parameters for complex systems (such as multi-ring, hydrocarbons) are unclear
and further development is required. Group parameters must be defined for parts
of the multi-ring compounds so that this method can be applied to these systems.
For non-polar and non-combined compounds, a certain functional group is
considered as a group, such as CH3, CH2 and etc. For high polarity or high
combination compounds, such as for DMSO, the whole molecule is considered as
a group since the interaction of the molecule is more than the Van Der Waals
interaction. For more complex multi-ring hydrocarbon systems, however, the
element which combines two rings is considered as a new group, ACC, and the
element which combines three rings is considered as another new group, AACC.
Naphthalene, for example, can be considered as 8ACH, 2ACC, while pyrene
considered as 10ACH, 4ACC, 2AACC.
The diffusion coeffcients at infinite dilution of alkane--aromatic hydrocarbon
systems, such as n-heptane--cumene(p-xylene, alpha-methyl naphthalene),
dodecane--naphthalene( phenanthrene, pyrene), were measured and the group
contribution parameters were evaluated in this paper . Experimental data from
references[5-8] were also utilized. The non-linearity Powell method was used to fit
the diffusing activation energies and diffusing area parameters. The evaluated
results are shown in Tables.
The chemicals used in the study had the following purity as reported by their
manufactures: toluene(>99.5%), cumene(>99.9%), p-xylene(>99.0%),
alphy-methyl naphthalene(>99.5%), naphthalene(>99.5%),
phenanthrene(>99.5%), pyrene(>99.5%). Water used in the experiment was
distilled water. A modified version of diaphragm cell technique[8] was used for
measuring the mutual diffusion coeffcients. A nickle alloy film with 35mm diameter
was used and the details of the apparatus have been described elsewhere[10].
The sample solution was analyzed by DMA60 vibration densimeter.
In order to test our apparatus, the diffusion coeffcients of toluene--DMSO system
were measured and compared with literature values[6]. The good agreement
between our data and the literature ones demonstrates that our experimental
result is reliable and accurate. The experimental diffusivities of selected
aromatics in DMSO at different concentration ranges are shown in Figures. The
UNIFAC model is used to evaluate the thermodynamic factor. The interaction
parameter of UNIFAC model can be obtained by fitting the LLE data respectively
for the systems such as toluene ( or naphthalene, alpha-methyl-naphthalene,
phenanthrene, pyrene etc.)--DMSO[11]. For cumene--DMSO systems, the
parameters are obtained from literature[12].
The diffusion coefficients of cumene( and alph-methyl naphthalene)--DMSO do not
change dramatically in the medium concentration range. It is found that the
thermodynamic factor changes slowly with the concentration of DMSO for the two
systems in the same medium concentration range. This indicates that the effect of
concentration on the diffusion coeffcient is determined by the thermodynamic
factor primarily if the difference of the viscosity of compounds in the solution is
small.
The effect of temperature and DMSO concentration on the diffusion coefficients of
naphthalene, phenanthrene, pyrene with DMSO at high DMSO concentration
range were discussed respectively. Furthermore, it is clear from the comparison
of the diffusion coefficients of aromatic hydrocarbons with different number at
cyclic groups (such as toluene, naphthalene, phenanthrene, pyrene) that their
diffusion coefficients in DMSO decrease with the numbers of cyclic aromatic
hydrocarbon groups and the increasing of length of the branched chain. This
may be caused by the molecular space structure and the viscosity of the
compounds.
In order to verify the effect of the thermodynamic factor on the diffusion
coefficient, the predicted results which evaluated from different interaction
parameters of UNIFAC model in the literature were compared with the
experimental ones. It is obvious that the deviations are large when the parameter
values from the literature[12] were used to calculate the thermodynamic factor. It
can be concluded that the thermodynamic factor has a significant effect on the
diffusion coefficients for these nonideal systems. It also indicates that a large
deviation will occur if the interaction parameters of UNIFAC model obtained from
the experimental data of monocyclic aromatic hydrocarbons are directly used to
predict the behaviors of polycyclic aromatic hydrocarbons.
It is concluded from this paper:
- The group contribution method for the prediction of diffusion coeffcients in liquids has been revised. A method of defining the functional groups has been suggested and the group parameter values have been evaluated.
- The concentration dependence of mutual diffusion coefficients has been determined for DMSO--aromatics( toluene, cumene, p-xylene, naphthalene, alpha-methyl naphthalene, phenanthrene and pyrene) systems at 25 oC, using the metallic diaphragm cell technique.
- The predicted diffusion coeffcients have been found to agree well with experimental data over a wide range of concentration and the major variation in the diffusion coefficient is shown to be due to the thermodynamic factor.
ACKNOWLEDGMENT
The State Key Laboratory of Chemical Engineering, China which supports this
research is greatly acknowledged. We are also very grateful to Prof. P. S. Ma,
Tianjin University for his helpful advice and discussions.
REFERENCES
- krishnamurthy, R., Talor, R., AIChE J., 31(3),449(1985)
- krishnamurthy, R., Talor, R., Ind. Eng. Chem. Pro. Des. Dev., 24(3),513(1985)
- Ye M., Ph D. Thesis, Tsinghua University, Beijing, 1988
- Ye, M., Fei, W. Y.,Dai,Y., Wang, J. D., Proceeding of ISEC'96, Vol.1,69, Univ. Of Melbourne, Australia(1996)
- Sanini, S.A. and Hutchison, P., J. Chem. Eng. Data,18,317 (1973)
- Thiel, P., Paschke, A. and Winkelman J., Ber. Bunsen-Ges. Phys. Chem., 96(6), 750 (1992)
- Dymond, J. H. , J. Phys. Chem., 85, 3291 (1981)
- Johnston, R.C., Lobdell, C.O. and Janauer, G.E., J. Phys. Chem., 83, 1816 (1979)
- Robinsn, R. L., Edmister, W. C. and Dullien, F.L., J. Phys. Chem., 69,258(1965)
- Yuan J., Ph.D. Thesis, Tianjin Unuversity, Tianjin,1986
- Cai Y., Bachelor Thesis, Tsinghua University, Beijing,1995
- Magnussen T., Rasmussen P. and Fredenslund A., Ind. Eng. Chem. Pro. Des. Dev., 20,331 (1981)
- Hayduk, W., Laudie, H. AIChE J. 20,611 (1974)
LYSOZYME EXTRACTION BY AOT REVERSED MICELLAR SYSTEMS USING A ROTATING DISC CONTACTOR - SIMULATION OF MASS TRANSFER PERFORMANCE
Jihong Tong1,* , Sosaku Ichikawa2, Shintaro Furusaki1 1 Graduate School of Engineering, The University of Tokyo, 7-3-1 Hongo, Bunkyo-ku, Tokyo 113, Japan 2 National Food Research Institute, Ministry of Agriculture, Forestry and Fisheries, 2-1-2 Kannondai, Tsukuba, Ibaraki 305, Japan
ABSTRACT
The mass transfer performance of lysozyme using AOT (di-2-ethylhexyl
sodium sulfosuccinate) reversed micellar systems formed in isooctane,
kerosene and silicone oil was investigated in a rotating disc contactor (RDC)
of 38 mm diameter.
The appropriate operating conditions of lysozyme extraction in RDC for the
three reversed micellar systems were determined by preliminary experiments.
The all experimental runs of lysozyme extraction in RDC were carried out
under room temperature. The concentration of AOT in organic phase was
maintained at 0.05 M in all experiments. The aqueous phase (0.2M KCl,
buffer solution, pH = 8.0) with lysozyme was used as the continuous phase,
and the reversed micellar organic phase was the dispersed phase. The two
phases flowed countercurrently in the RDC. Lysozyme transferred from the
continuous to dispersed phase. The lysozyme concentration profiles along
the RDC were measured by taking and analyzing two phase samples,
respectively.
The diffusion model was used to simulate the extraction performance. The
model was solved numerically by changing parameters to fit the calculated
two phase concentration profiles with the meásured profiles using the
Complex optimizing method. The axial dispersion coefficients of two phases
and the overall mass transfer coefficients based on the continuous phase in
the RDC were determined as parameters.
Also, the axial dispersion coefficients and the overall mass transfer
coefficients were predicted by using previous correlations. Under the
experimental conditions of this study, it was assumed that the mass transfer
process of lysozyme extraction by reversed micellar systems was controlled
by the diffusion of the protein in the aqueous phase boundary layer. The
interfacial resistance was not important in the protein extraction process. It
was also assumed that the reversed micellar dispersed droplets were stagnant
spheres because of the present of surfactant. The overall mass transfer
coefficients of lysozyme from the aqueous phase to the reversed micellar
dispersed phase were calculated by combination of some previous
correlations under these assumptions. The predicted results were compared
with those obtained from the diffusion model solution. The values of mass
transfer coefficients obtained from the diffusion model agreed with those by
the previous correlations in the literatures fairly well.
It is suggested that the diffusion model may be used for the mass transfer
prediction and the column design for the reversed micellar extraction of
proteins.
* Jihong Tong is now working in Soken Chemical & Engineering Co., Ltd., Japan
|